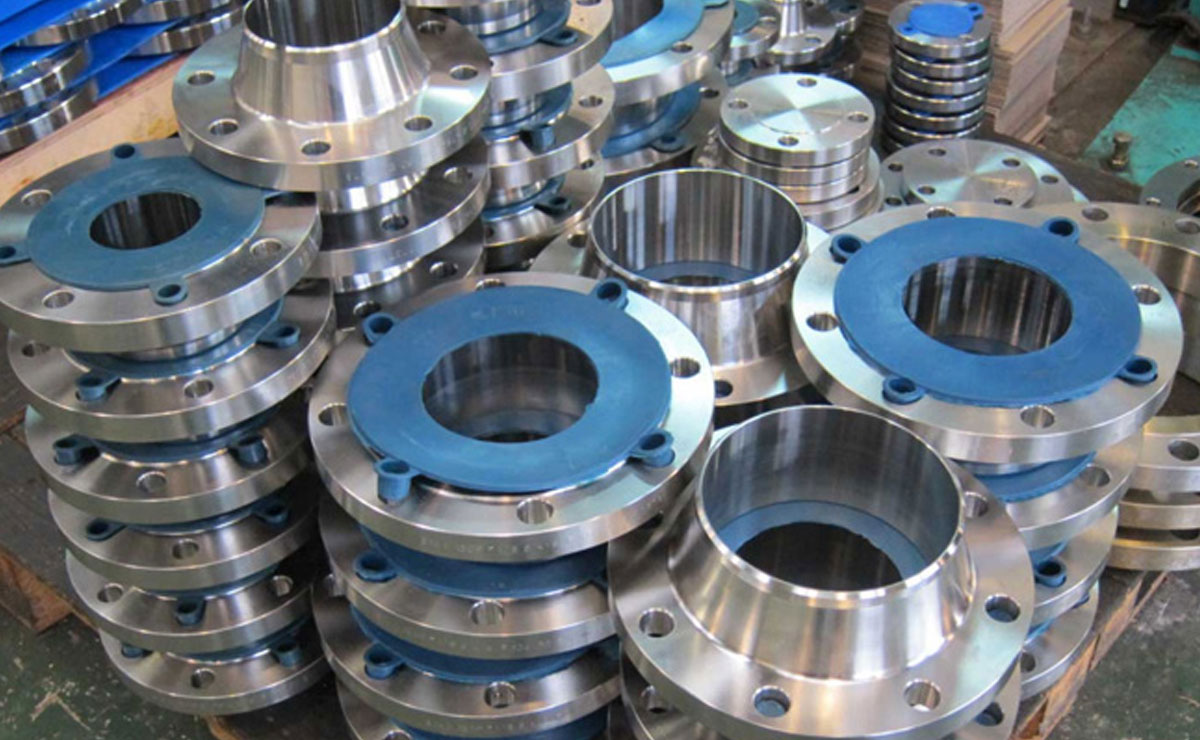
A flange is a forged or cast ring of steel designed to connect sections of pipe or join pipe to a pressure Vessel, pump or any other integral flanges assembly. Flanges are joined to each other by bolting and joined to the piping system by welding or threading. The basic types of flanges are; Stainless Steel Flanges (ss Flanges), Alloy steel flanges, Carbon steel flanges, Slip on, Blind, Weld Neck, Threaded, Socket Weld, Lap Joint and Orifice.
Flanges are designed to the following pressure ratings : 150lb, 300lb, 400lb, 600lb, 900lb, 1500lb and 2500lb.
The most common facings machined on flanges are:
(a) Raised face, 1/16 inch for 150lb and 300lb, ¼ inch for 400lb and heavier.
(b) Flat face, for 150lb and 300lb only, other may be flat face on request.
(c) Ring type joint, may be applied to all pressure ratings.
Flanges are designed to the following pressure ratings : 150lb, 300lb, 400lb, 600lb, 900lb, 1500lb and 2500lb.
The most common facings machined on flanges are:
(a) Raised face, 1/16 inch for 150lb and 300lb, ¼ inch for 400lb and heavier.
(b) Flat face, for 150lb and 300lb only, other may be flat face on request.
(c) Ring type joint, may be applied to all pressure ratings.
Applications of Stainless Steel Flanges
- Pipeline engineering
- Oil & gas industry
- Mechanical engineering
- Plant engineering
- Marine industry
- Waste water management
- Chemical industry
- Petrochemical industry
- Power industry
- Aerospace
- Food processing industry and many more.
Advantages:
- Resistant to corrosion and staining
- Low maintenance
- Bright familiar luster
- Steel Strength
Types of Flanges
– Our manufacturing facilities are well equipped to manufacture various types of flanges, namely:
- Blind FlangeA Blind flange is a round plate that has all of the relevant boltholes but no centre hole, and because of this, it is used to close off the ends of piping systems and pressure vessel openings. It also permits easy access to vessels or piping systems for inspection purposes.
- Weld Neck FlangeWeld Neck flanges have a long tapered hub and are often used for high-pressure applications. These flanges are designed to be joined to a piping system by bun welding. The neck or hub transmits stresses to the pipe, reducing stress concentrations at the flange base. The gradual thickness transition from the hub base to the wall thickness at the bun weld provides critical flange reinforcement. The bore of the flange matches the bore of the pipe, reducing turbulence and erosion. These flanges are ideal for extreme temperature fluctuations and environments where there may be high pressure..
- Slip-on FlangeThese are easily fitted and welded into different pipes. A slip-on pipe flange is slipped over the pipe and then welded both inside and outside to provide sufficient strength and prevent leakage. These flanges are ideal for lower pressure applications. It is used in preference to weld necks by many users because of its lower cost and the fact that less accuracy is required when cutting pipe to length..
- Socket Weld FlangeThese flanges are attached by inserting the pipe into the socket end. It allows for a smooth bore and a better flow of the fluid or gas inside. Socket-weld pipe flanges are mainly used for smaller sizes of high-pressure pipes.
- Threaded FlangeThreaded flanges are similar to slip-on pipe flanges except for the bore of threaded pipe flange has tapered threads. These flanges are ideal for relatively low-pressure piping systems. Threaded flanges are used with pipes that have external threads. The benefit of these pipe flanges is that they can be attached without welding.
- Lap Joint FlangeLap Joint Flanges slide over the pipe and are most commonly used with stub end fittings. A pipe is typically welded to the stub end, and the lap joint pipe flange is free to rotate around the stub end. Lap Joint pipe flanges are often used for applications that require frequent dismantling. Threaded pipe flanges are often used for small diameter, high-pressure requirements.
- Orifice FlangeOrifice Flanges are used instead of standard pipe flanges when an orifice plate or flow nozzle must be installed. Pairs of pressure tappings are machined into the orifice flange, making separate orifice carriers or tappings in the pipe wall compulsory. In addition to these, we also manufacture Orifice Flange, Stub-end fittings, plate flanges, backup flanges, Beveled ID flanges and Reducing flanges.